Locally sourced: using site subsoil as a construction material
Every year in the UK, over 23m tonnes of excavated soil is sent to landfill from construction sites, at a cost to the environment, the developer and society. Yet, earth is one of our most sustainable building materials that could replace carbon intense products.
Earth blocks use excavated clay from the construction site mixed with sand and straw to produce unfired bricks for the new development. Unlike standard blockwork, which has limited recycling potential, earth blocks can be broken down and reused, or returned to nature at the end of their lifespan. As such, the earth block can store the building resource within the walls of the development throughout the lifetime of the building. This living material also brings climatic benefits to buildings – it regulates indoor temperature and humidity levels, and purifies the air by trapping airborne pollutants.
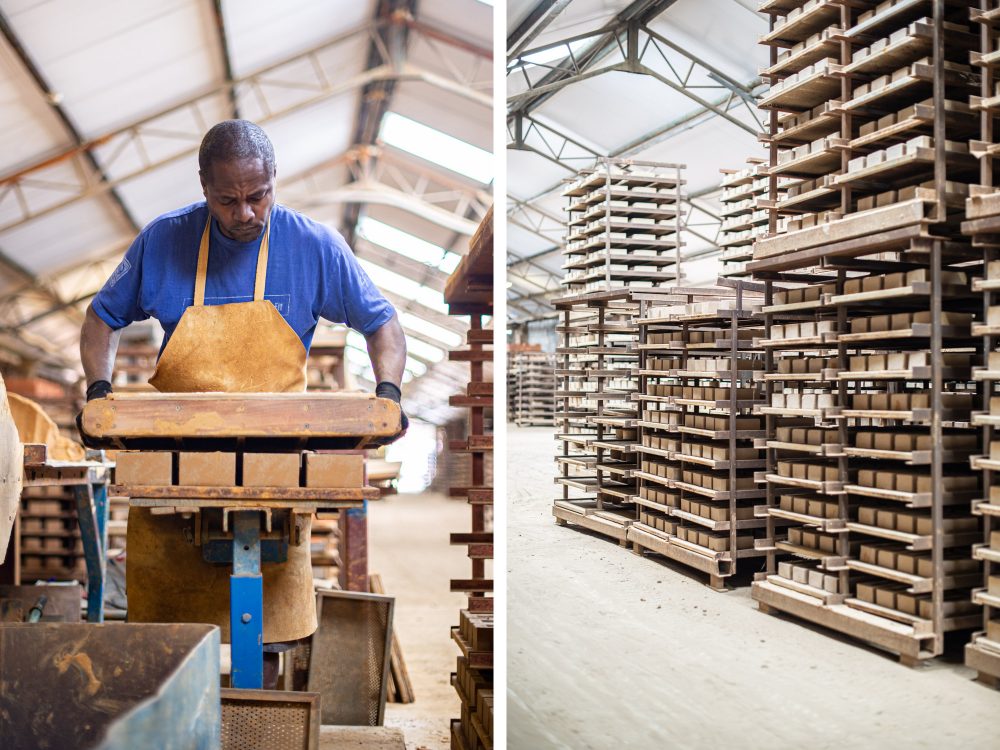
Reef Group are incorporating earth blocks made from the excavated subsoil in the lower levels of The Apex building, the initial phase of the Tribeca neighbourhood, in an conscious effort to bring regenerative materials into larger scale commercial projects where they have the greatest impact. If successful, the trial could be scaled up to exceed sustainability targets and set a precedent for the UK construction industry.
The Journal met with Nikolay Shahpazov, architect at Bennetts Associates, to learn more about the benefits of unfired earth blocks.
The Tribeca development has a strong sustainability agenda. Could you summarise the commitment to use climate friendly building materials and construction methods.
Nikolay: The project is targeting very high BREEAM scores and various other certifications, but the earth blocks brings another dimension to this ambition, because most of the current sustainability certifications don’t necessarily deal with the embodied carbon of materials. Earth blocks has one tenth of the embodied carbon of other commonly specified materials such as blockwork, which is a cement-based product. Aside from the high energy demand during production, blockwork and concrete manufacturing consumes large quantities of sand, which has led to fast depleting sand supplies and environmentally damaging sea extraction. The low embodied carbon of earth blocks is a great starting point that positions us ahead of what most commercial developments are committing to right now.
Tell us about the process from excavation to construction, and the particular properties of the Tribeca earth block.
Nikolay: We sample the soil in various corners of the site and test this as an earth block mix with HG Matthews, the material manufacturer. Sometimes the excavated material can be contaminated and require treatment, but the soil is pure deep underground even on previously developed land. The deeper strata of the King’s Cross soil is very stiff clay that produces very strong earth block. Once the mix is determined the product will be assessed to specify the technical performance before scaling up production. At least 60% of the excavated earth can normally be used, saving the developer expensive land fill tax.
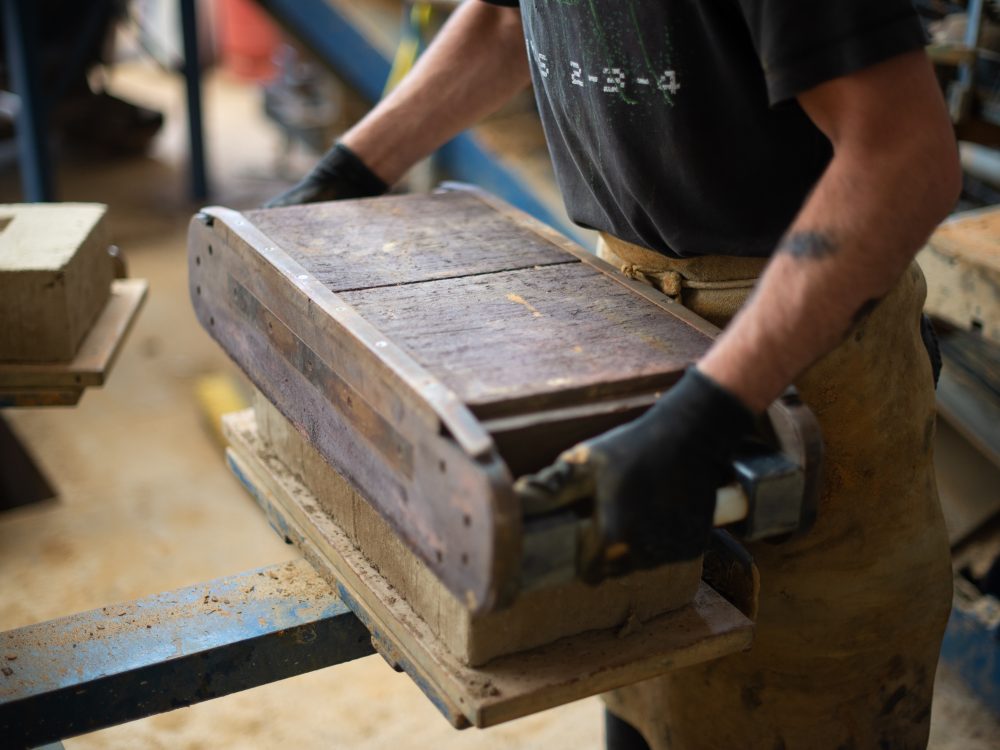
How will the product be integrated into the development, and blended with more high tech materials and solutions?
Nikolay: For The Apex, the earth blocks are used exclusively in the basement in place of concrete blockwork. Earth blocks can be used as load bearing elements for smaller buildings, but because they are unfired, they are weaker than blockwork, requiring a different approach to structural engineering.
There are other manufacturing techniques using dynamic compaction that can produce denser blocks almost twice as strong. Austrian earth construction specialist Martin Rauch has developed an automated method of manufacturing off site rammed earth cladding panels that achieve significant carbon reductions. Increasing the strength and usability of the product will unlock more design opportunities and architectural expressions. It is an incredible material with a tactile quality that connects us with the earth and ancient geological processes. I think it is really beautiful.
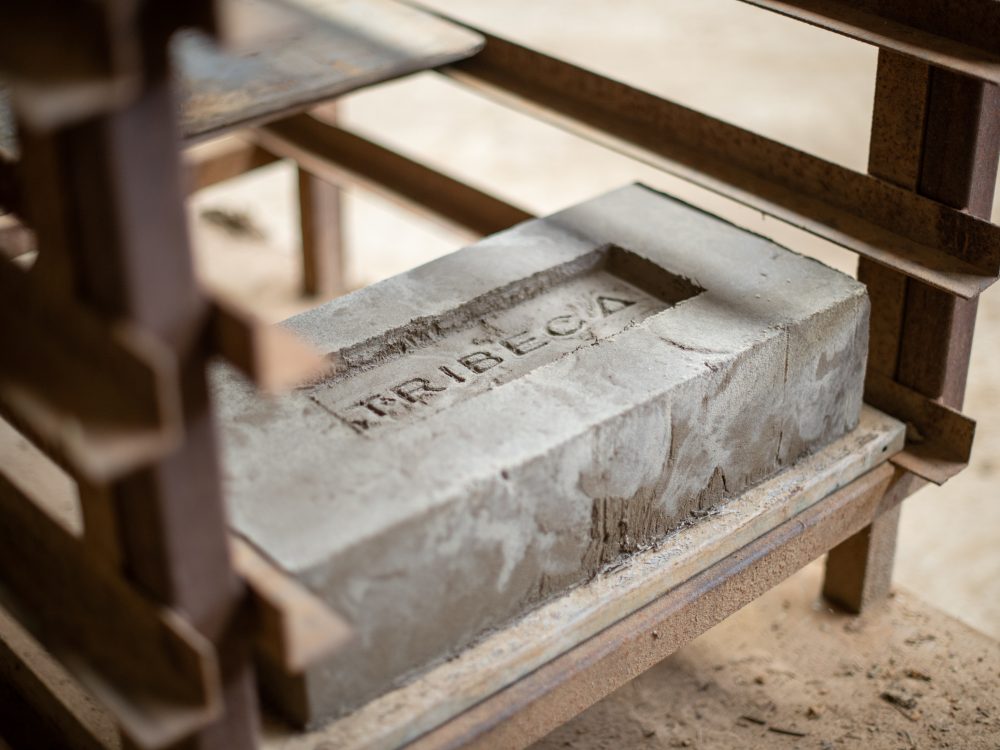
How do earth blocks compare to standard cement/fire clay block in terms of technical performance, durability and cost?
Nikolay: For something so innovative that is not yet in widespread use, the cost is very comparable in price to blockwork construction. Developers also save on the landfill tax by using the soil on site, and if it’s possible to bring manufacturing closer to site, there is additional cost reduction benefits. Strength wise, it is probably half the compressive strength of blockwork, but in many situations that extra strength is not needed. They are different to commercialised products, but any limitations can be overcome and don’t prevent the material from meeting the performance criteria of the building.
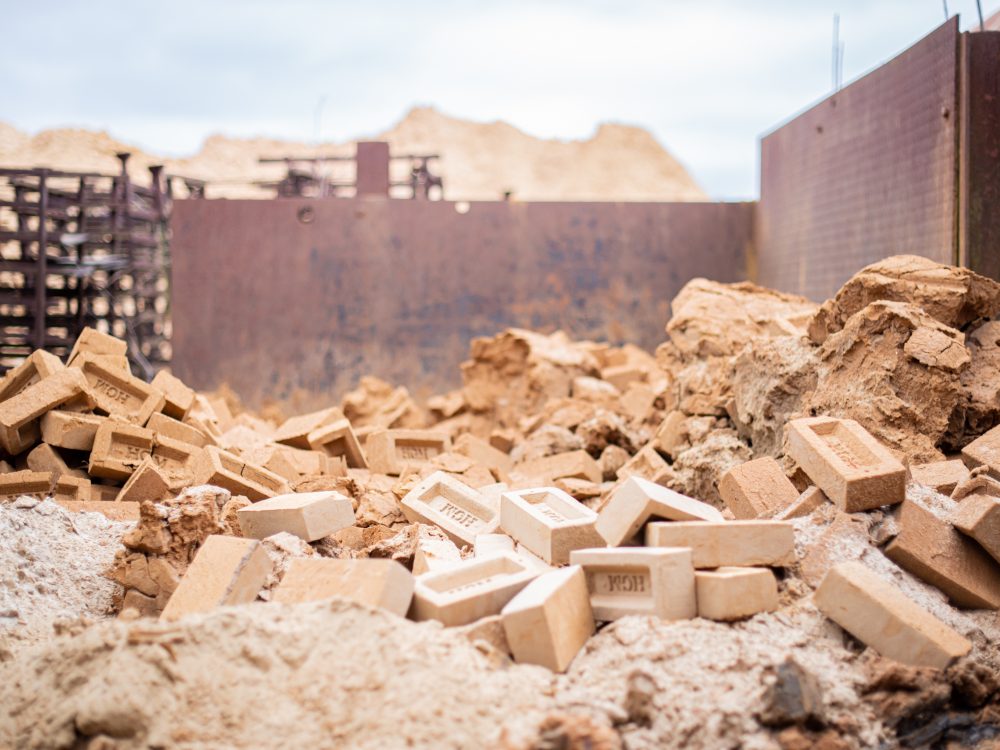
‘Earthcycle: Earth blocks from subsoil’ produced by the team at Bennetts Associates will be exhibited in the Royal Academy of Arts’ Architecture Summer Exhibition where it will inform wider audiences about the financial and environmental benefit of utilising site subsoil as a construction material.