A circular approach to materiality
The UK construction industry uses over 400 million tonnes of materials annually [1], which makes it the largest consumer of natural resources in the country. In the traditional take-make-waste construction model, 54% of demolition materials go to landfill [2] at a huge cost to the environment, society, and the developer.
In a quest to do things differently, The Reef Group has committed to recycle or reuse 95% of the waste from the existing buildings on the site, and are currently diverting 99% of waste from landfill. As the defunct buildings are dismantled, functional materials are reused, and end of life materials are returned to the market as a renewable resource, proving that in our world of finite resources, circularity can produce an abundance of materials without environmental degradation.
The built environment sector is moving beyond just responsibly sourced materials, to embed reuse and recycling as part of their ESG agenda, responding to consumer demands and aligning with the UN’s Sustainable Development Goals for sustainable cities and communities, responsible consumption and production, and climate action. Coupled with a decarbonised supply chain, the transition to a circular construction model is an important step towards addressing greenhouse gas emissions, waste, pollution, and climate change.
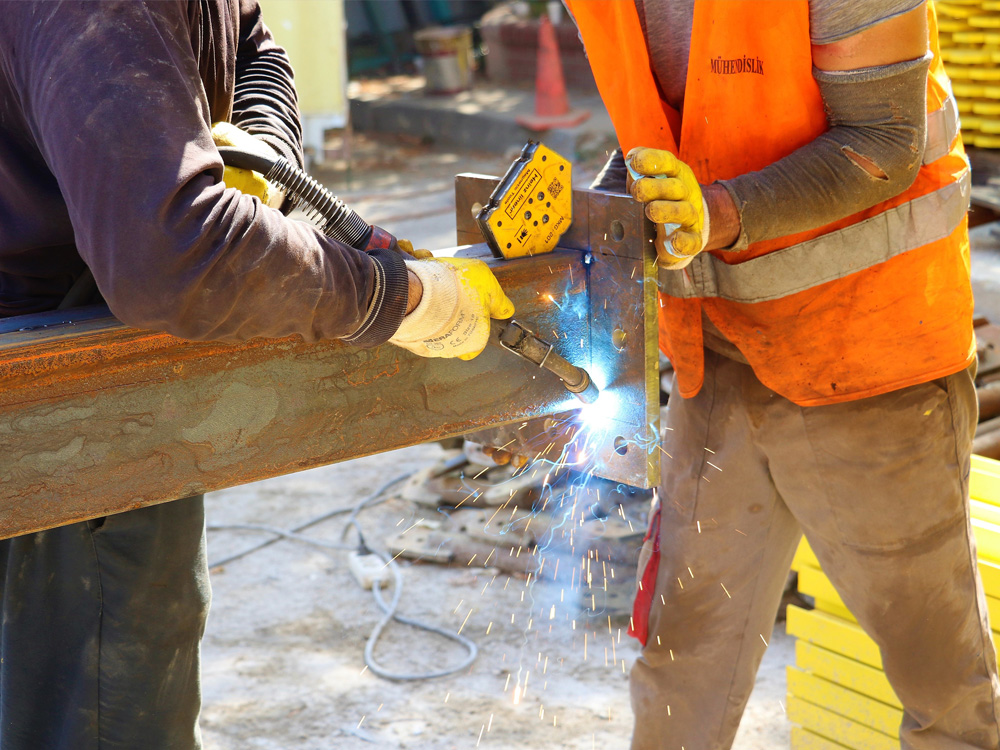
Reusing materials from the site is one of the most sustainable options available to developers, minimising processing, refining, and logistics while reducing the dependency on virgin materials. Working with a hyper-local pool of available raw materials and components, the supply chain is simplified and shortened, which provides greater insight into the production and manufacturing process to ensure that it is sustainable and ethical.
In the Apex Building, the first phase of the Tribeca development which is due for completion this year, the basement is partly constructed with Earth Block cast from excavated subsoil from the construction site, which produces a building component that can be deconstructed and reused at the end of its lifecycle, or returned to nature.
From the 20,000 tonnes of concrete that has been removed from the site, the rebar will be recycled and the concrete crushed and used to create the piling mat. The existing steel will be installed as structural elements during temporary works, and as permanent building elements in the new development; the central Pavilion will be constructed using some of the salvaged steel from the site.
Leftover materials won’t go to waste either. Surplus steel is sent to a local supplier that processes, remanufactures and certifies the material for reuse in other schemes, and surplus concrete is reused as aggregate in other products – a great win for the construction industry where concrete accounts for nearly 8% of global greenhouse emissions [3].
Whilst the existing buildings have reached the end of their life, the individual components are granted a second life, facilitated by new perspectives, technologies, and processes that unlock the potential for reuse. With comprehensive circular strategies in place, it is anticipated that the construction industry can boost its circularity to 50% and cut greenhouse gas emissions by 52% [4], disrupting the traditional model and paving the way for a more responsible and sustainable built environment.